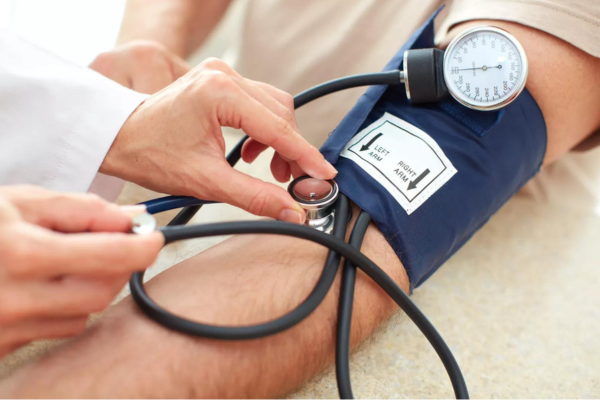
In the medical device industry, the design and selection of seals are crucial for ensuring the safety, reliability, and functionality of devices. Seals in medical devices prevent contamination, maintain pressure, and protect sensitive components from environmental factors.
Given the critical nature of these devices, every aspect of seal design requires careful consideration. This guide explores the key considerations for designing seals in medical devices, covering material selection, design factors, regulatory compliance, and testing protocols.
Understanding the Importance of Seals in Medical Devices
Used in a wide range of medical devices Seals, from simple syringes to complex surgical instruments and implantable devices. They serve multiple purposes:
- Preventing Contamination: Seals help keep out bacteria and other contaminants that could compromise the sterility of the medical device.
- Ensuring Functionality: For devices that operate under pressure or vacuum conditions, seals maintain the necessary environment for device operation.
- Protecting Components: Many medical devices contain sensitive electronics; seals protect these components from moisture and other damaging environmental conditions.
Material Selection for Medical Device Seals
Choosing the right material is the first critical step in seal design. The material must be compatible with the device’s operating environment and the media it will be exposed to, such as bodily fluids, cleaning agents, or sterilization processes. Key considerations include:
- Biocompatibility
The material must not cause any adverse reaction when in contact with the body or bodily fluids. Silicone, for example, is commonly used because of its excellent biocompatibility and flexibility.
- Chemical Resistance
Seal materials need to withstand exposure to various chemicals, including pharmaceuticals and sterilization agents. Materials like PTFE (Polytetrafluoroethylene) and EPDM (Ethylene Propylene Diene Monomer) are popular choices for their strong chemical resistance.
- Physical Properties
The strength, elasticity, and durability of the seal material are important, especially for devices that undergo repeated use and sterilization. The material must maintain its integrity over time without degrading.
Design Factors in Seal Configuration
The design of the seal is equally important as the material choice. The design must account for the shape, size, and fit of the seal within the device, as well as the specific mechanical and environmental stresses it will encounter.
- Tolerance and Fit
Precision in dimension and fit is crucial to ensure that the seal properly fits into the device without being too loose or too tight. Poorly fitting seals can lead to leaks and device failure.
- Load and Pressure Requirements
The seal design must consider the load and pressure that the seal will need to withstand. This includes dynamic loads for moving parts and static loads in stationary applications.
- Assembly and Installation
The design should also consider ease of assembly and the potential for damage during installation. A complex seal design might offer better performance but could be more prone to installation errors.
Regulatory Compliance and Standards
All medical devices must comply with stringent regulatory standards to ensure safety and efficacy. Seals are no exception. Compliance with standards such as ISO 13485 for medical devices helps ensure that seals meet international safety requirements. Additionally, the U.S. Food and Drug Administration (FDA) sets guidelines for materials and designs used in medical devices, which must be followed.
Testing Protocols for Medical Device Seals
Testing is a critical phase in the development of Medical Devices Seals. These tests simulate the conditions the seals will face in actual use to ensure they meet all performance criteria.
- Leak Testing
Leak tests are performed to ensure that the seal completely prevents any unintended ingress or egress of fluids or gases.
- Aging and Fatigue Testing
These tests assess how the seal material and design hold up under repeated use and over time, particularly when exposed to cycles of sterilization and usage.
- Chemical Compatibility Testing
This testing ensures that the seal material does not degrade or react when exposed to chemicals it will encounter during its lifespan.
Conclusion
Designing effective medical device seals is a complex process that requires a thorough understanding of materials science, mechanical engineering, and regulatory requirements. The right choice of material, precise design considerations, strict adherence to regulatory standards, and comprehensive testing protocols are all critical to ensuring that the seals perform their essential functions throughout the device’s lifespan. By meticulously addressing each of these aspects, manufacturers can ensure that their medical devices are safe, reliable, and effective in meeting the needs of the healthcare industry. Thank visiting Thank visiting incnewsblogs.com