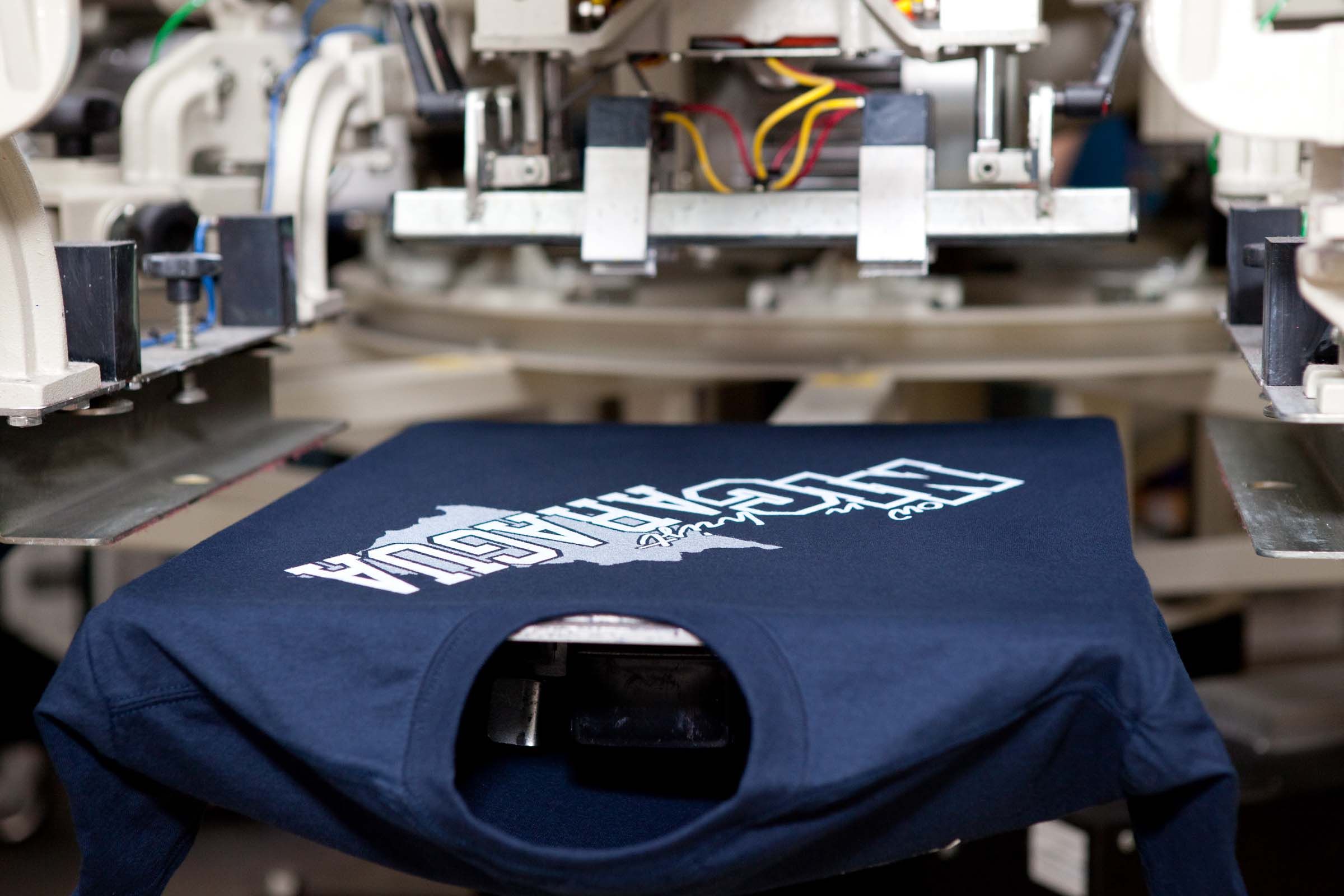
Direct-to-Garment (DTG) printing has emerged as a game-changer in the realm of custom apparel, offering unparalleled precision, vibrancy, and versatility in printing designs directly onto shirts. From intricate artwork to vibrant graphics, DTG printing enables the creation of highly detailed and visually striking garments. In this comprehensive guide, we’ll delve into the intricate process of direct to garment shirt printing, exploring each step in detail and shedding light on the techniques, tools, and considerations involved.
Design Selection and Preparation:
The journey of custom shirt printing with DTG begins with design selection and preparation. Clients collaborate with designers or utilize design software to create or upload their designs. These designs should be high-resolution, properly sized, and saved in the appropriate file format (usually JPEG, PNG, or PDF) for compatibility with DTG printing software.
Pre-Treatment Process:
Before printing can commence, the shirt undergoes a pre-treatment process to optimize ink absorption and color vibrancy. A pre-treatment solution is applied to the fabric using specialized spraying or coating equipment. This solution helps the ink adhere to the fabric fibers and prevents bleeding or fading during printing. Proper pre-treatment is crucial for achieving vibrant colors and crisp details in the final print.
Printing Setup:
With the shirt pre-treated, it’s ready for printing setup. The design is loaded into the DTG printer’s software, and any necessary adjustments are made to the print settings, such as color profile, resolution, and ink density. The shirt is then placed on the printer’s platen, ensuring it’s flat and positioned correctly for printing.
Printing Process:
The DTG printing process begins with a white base layer of ink, which serves as a foundation for the colors in the design. The printer’s printhead moves back and forth across the shirt, depositing the colored inks onto the fabric in precise layers to create the desired design. DTG printers can print millions of colors, gradients, and intricate details, making them ideal for complex designs and photographic prints.
Post-Treatment and Curing:
After printing, the shirt undergoes post-treatment to set the ink and ensure durability. This may involve heat curing the shirt in a conveyor dryer or heat press machine, which helps the ink bond with the fabric and withstand washing and wear. Some printers also offer additional post-treatment options, such as applying a protective coating or sealant to enhance color fastness and longevity.
Quality Control:
Quality control is a critical step in the DTG printing process to ensure each shirt meets the desired standards of excellence. Shirts are inspected for color accuracy, print clarity, registration alignment, and overall quality before being deemed ready for packaging and delivery. Any imperfections or inconsistencies are addressed and corrected to ensure customer satisfaction.
Conclusion:
Custom shirt printing using the DTG printing method offers unmatched precision, vibrancy, and customization options, making it a preferred choice for individuals and businesses seeking high-quality printed apparel. By understanding the intricate process involved—from design selection to post-treatment and quality control—customers can create vibrant, detailed prints that captivate and impress. With its ability to reproduce complex designs with stunning accuracy, DTG printing continues to redefine the possibilities of custom apparel customization and innovation.